Let's Think the Way We Build—in 3D
June 21, 2023
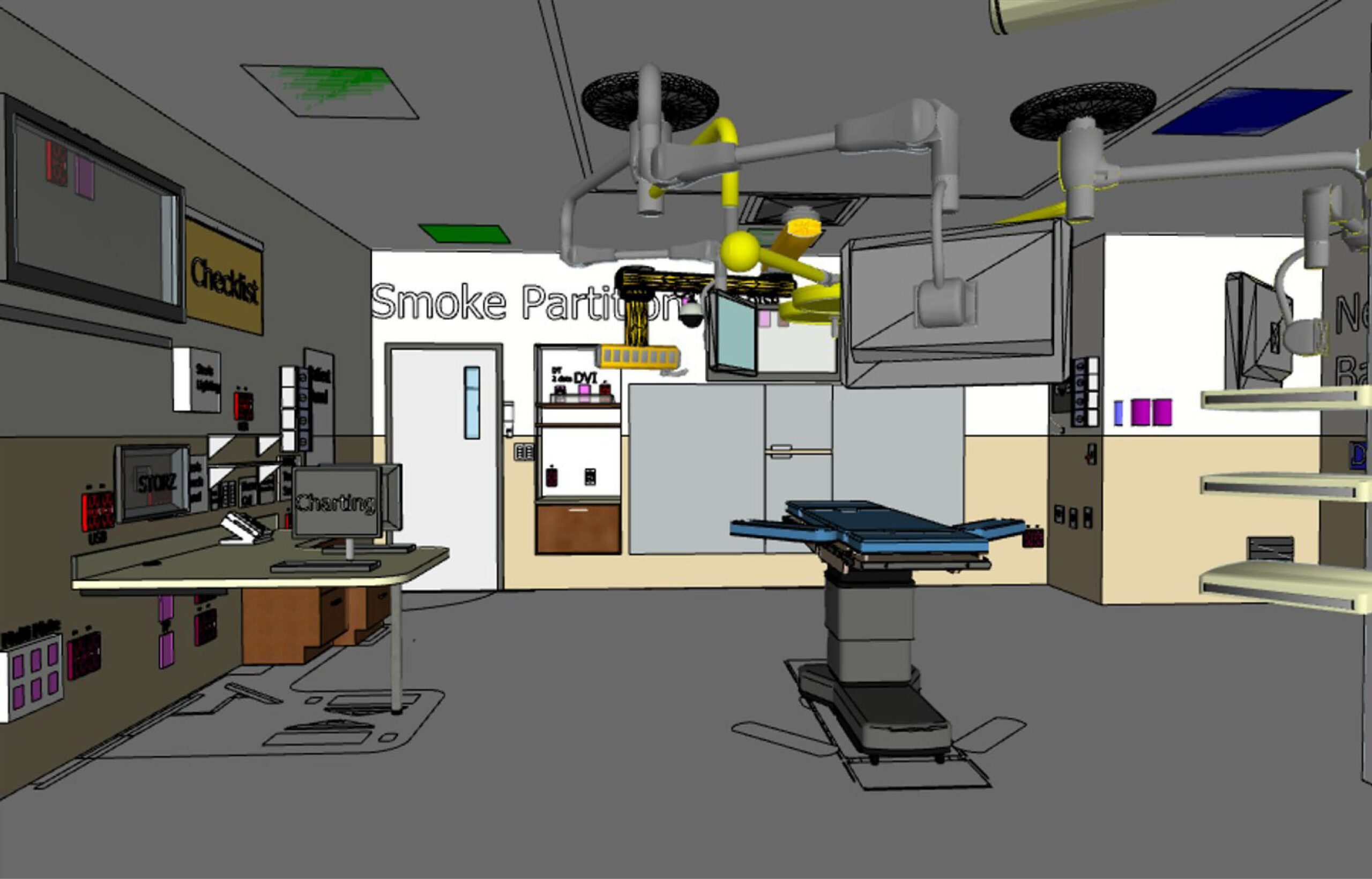
How Virtual Mock-ups Drive Innovative and Collaborative Decision-making on Sophisticated Health Care Construction Projects
By: Paul Schmidt, Operations Vice President and Columbus Region Leader at Messer
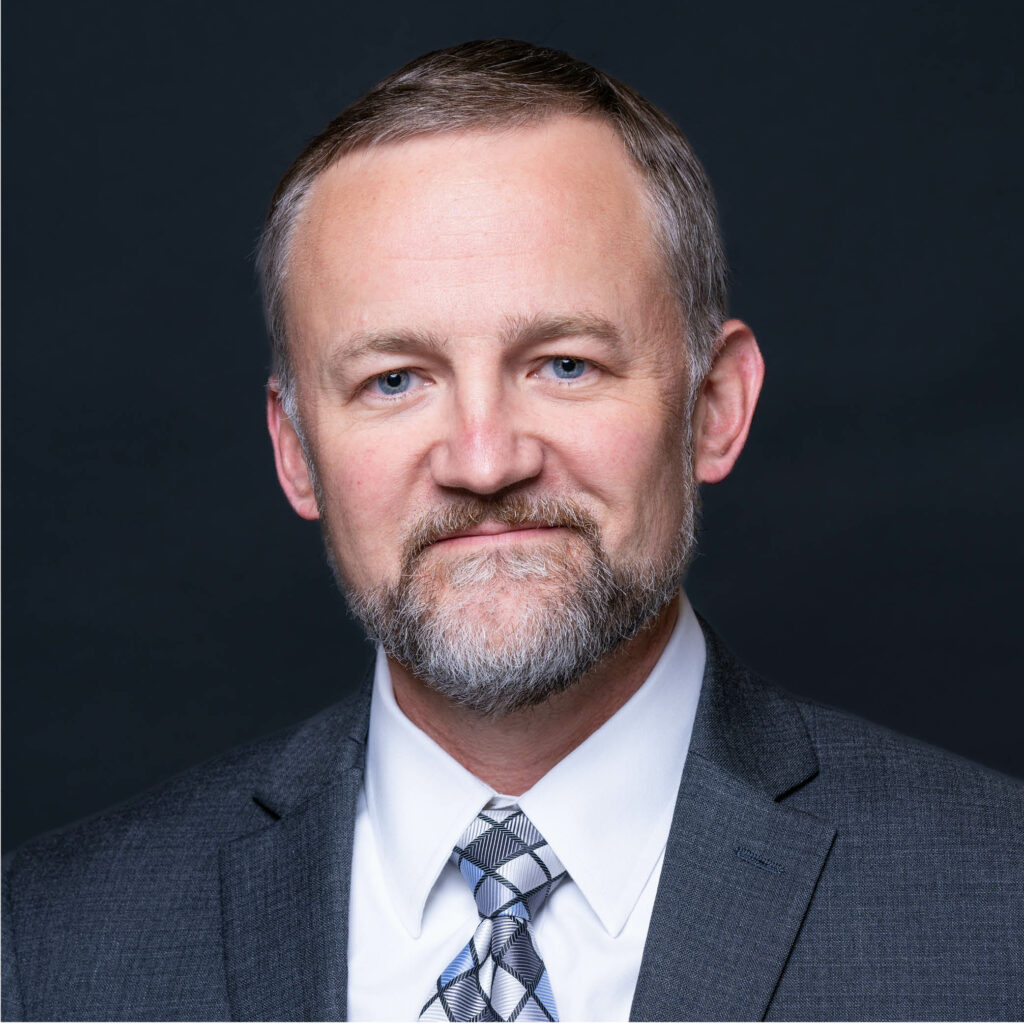
Paul Schmidt, Operations Vice President and Columbus Region Leader at Messer
One downside to becoming a true professional in your field is that it can give you tunnel vision and the false assumption that everyone else possesses equal knowledge. Even the best explanation from a physician won’t help me understand a patient’s chart to the point where I can confidently map out the treatment he or she needs.
The same is true when health care leaders embark on construction projects. They can sit down with a talented designer and agree on the layout of a PACU or operating room, but still be left wondering where the case cart is supposed to go after the project is turned over (leading to late-stage rework). Where’s the disconnect? Typical construction drawings are often compiled in a way that feels like a scavenger hunt to find the entire scope of work.
When you bring all the details together in a virtual mock-up of the space, end users are better positioned to speak up about the things they don’t see, or that won’t work in real life. Good architects facilitate this process during the design stage, but it shouldn’t stop there.
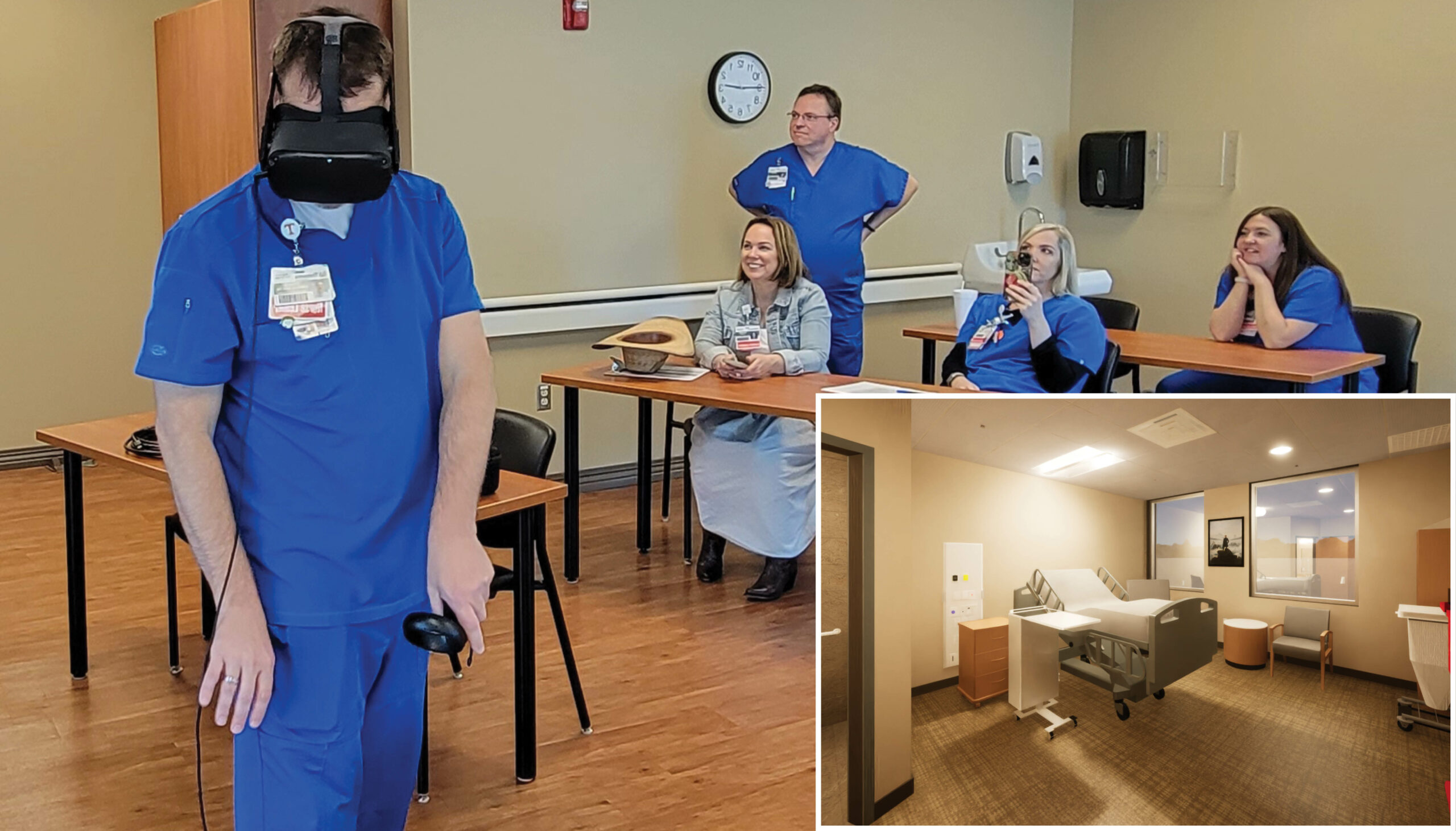
Preparation Pays Off
On the health care projects Messer leads, it’s incredibly valuable to virtually mock up everything that we intend to build, including furniture and equipment that we may not be responsible for procuring or installing. We can’t get an accurate picture without capturing everything that belongs in the space—correctly sized and easily identifiable.
This may sound time-consuming, but I prefer to classify it as “tradeoff time” carrying no extra cost for the client. We’re proactively planning work rather than reactively wasting time dealing with questions and conflicts in the field and resolving changes at the end of a project. It’s not an extra step; it’s a tradeoff that delivers more reliable results and can positively impact the schedule, budget and quality.
For example, on a steam plant renovation for a laboratory building, it was presumed we could only sequence work a certain way based on 2D drawings, thus dictating the original schedule. We took the time to draw a full 3D model of the new boilers and combined it with a point cloud scan of the existing plant to see if we could install an additional boiler in an earlier phase. It seemed impossible in 2D, but the 3D mockup validated the idea and we were able to complete the project an entire year early due to the additional steam capacity created by that one boiler getting installed before the rest of the demolition was complete.
Details Matter
No two health care facilities function exactly the same, so we can’t afford to overlook small, but important, details such as the quantity of power outlets, the location of light fixtures, where systems and signage will be mounted on the ceiling, and how wall protection trim may interfere with other devices at a certain elevation.

No project team wants to be saddled with that rework and the accompanying costs and schedule delays, so we ensure the model is accessible to field leaders for the duration of the job. Think of it as a dynamic, illustrated “instruction manual” for executing the work that leads to direct accountability onsite and a higher quality end product—not just a flashy model to show off once and then relegate to a file folder.
More Input Yields Better Decisions
This raises an important point about not making decisions in a vacuum. It’s critical to solicit trade contractors’ feedback and make room for creative solutions to be presented. The virtual mock-up process gives us all an opportunity to think through the means and methods, as well as propose tweaks to the exact placement of items that, for example, could allow electrical and plumbing contractors to complete rough-ins more efficiently or prefabricate portions of their work offsite.
The collaboration must extend to end users, too. Nobody should approve a design and cross their fingers that everything will be perfect when the building opens months or years later. At the same time, health care workers’ time is best spent caring for patients, not staring at drawings they can’t fully understand.
A detailed virtual mock-up reinforces what’s about to be built in a more consolidated way and offers owners a chance to confirm it’s what they want, or to make some final clarifications. The goal isn’t to question the design; it’s to coordinate everything being purchased and installed so clients get precisely what they need.
I always feel more confident making decisions when they’re based on knowledge verified by a team of experts. Virtual mock-ups help contractors understand how to build the space and help owners understand how they’ll use the space to support their mission: providing a high-quality, compassionate health care experience.